KPIs para la gestión de mantenimiento
Con el paso del tiempo y el uso es inevitable que una máquina o equipo sufra problemas de degradación. Si estos problemas no son atendidos, el rendimiento, la vida útil y capacidad de los equipos para funcionar como se espera, se verán afectados negativamente.
Este es un problema que sufren muchas empresas con instalaciones de máquinas o equipos. Sin embargo, si deseamos tener una tasa de utilización alta, debemos tener un buen sistema de mantenimiento que procure prolongar el funcionamiento continúo de las instalaciones, reducir costos, alargar la vida útil de cualquier máquina, evitar pérdidas, entre otros.
Una buena práctica en la gestión del mantenimiento es el uso de datos para la toma de decisiones. Una manera de hacerlo es utilizando indicadores clave de rendimiento para la planificación del mantenimiento, los cuales nos permitirán rastrear información relevante como el número de órdenes de trabajo por atender, el tiempo medio de reparación, disponibilidad de equipos, entre otros.
Es por eso que si en tu empresa deseas identificar áreas de oportunidad, optimizar recursos y sobre todo, garantizar la fiabilidad de los equipos; debes comenzar a diseñar, implementar, programar y realizar el seguimiento de KPIs que te permitan realizar una eficiente gestión del mantenimiento.
Hoy hemos preparado un listado de KPIs para la gestión de mantenimiento. Puedes tomar algunos de ellos como una base para comenzar o integrarlos a tu sistema de mantenimiento actual. ¡Esperamos que te sirvan!
¿Sabías qué? Según un Informe de Gestión de Mantenimiento Global (2023) de ABL Group, un 43.48% de los gerentes de mantenimiento indican que el segundo KPI de máxima prioridad es la disponibilidad y el tiempo de funcionamiento de los equipos.
Indicadores clave de desempeño en la gestión de mantenimiento
Antes de presentar los KPIs de mantenimiento, es importante tener en cuenta una cosa: cada organización debe definir sus indicadores de gestión.
En la literatura se pueden encontrar decenas de indicadores. Sin embargo, lo que realmente es importante es que se apliquen los métodos necesarios para diseñar un indicador que aporte valor agregado a la empresa y al trabajo de las personas, dándoles dirección a los procesos con el fin de saber si van por buen camino o no, y así tomar acciones de mejora.
-
Tiempo medio entre fallas (MTBF)
Es la media de tiempo entre fallos reparables de un equipo. Es utilizado para controlar la disponibilidad y fiabilidad de un equipo. Cuanto mayor sea el tiempo entre fallos, más fiable será el sistema.
El objetivo de las empresas respecto a este indicador debe ser buscar mantener un tiempo medio entre fallas lo más alto posible, es decir, que transcurran miles de horas entre las incidencias.
El tiempo medio entre fallas se calcula de la siguiente manera:
50 máquinas operaron durante 24 horas durante 350 días de un año y se registraron en ese período 15 fallos para todas esas máquinas.
MTBF = (50 * 24 * 350 Hrs.) / 15 fallos = 420,000 Hrs. de operación / 15 fallos
MTBF = 28,000 hrs.
Este es uno de los KPIs en la gestión de mantenimiento más importante, esto debido a:
> Evalúa la confiabilidad de los equipos: mide el tiempo promedio que un equipo puede operar sin fallas.
> Ayuda a planificar el mantenimiento preventivo: permite anticiparse a posibles fallas.
> Reduce los costos operativos: las empresas pueden optimizar la frecuencia de los mantenimientos, evitando reparaciones innecesarias y prolongando la vida útil de los equipos.
-
Tiempo medio para reparación (MTTR)
Es el valor promedio de tiempo de cada reparación. Mide la rapidez con la que un equipo puede ser reparado y volver a estar operativo.
El tiempo medio para reparación se calcula de la siguiente manera:Supongamos la siguiente situación: 3 equipos estuvieron detenidos por mantenimiento correctivo, el primero por 2 fallas por un total de 4 horas, el segundo por 1 falla durante 2 horas y el tercero 3 fallas por 6 horas.
MTTR = (4 + 2 + 6 horas) / 6MTTR = 2 hrs.
El tiempo medio para reparación es importante para las organizaciones que tengan equipos o brinden servicios de mantenimiento, pues su monitoreo permite conocer:
> El tiempo de inactividad: a la empresa que lo utilice le permite saber cuánto tiempo le toma reparar un equipo
> La eficiencia del equipo técnico: refleja que tan eficientemente el equipo de mantenimiento responde a las fallas. Por ejemplo, un tiempo de reparación bajo, puede indicar que el personal técnico está capacitado, tiene acceso a las herramientas necesarias y sigue procedimientos efectivos para solucionar problemas.
> Cuellos de botella en el proceso de reparación: el MTTR elevado puede señalar ineficiencias en el proceso de reparación. -
Tiempo medio para fallar (MTTF)
Mide el tiempo promedio que se espera que un equipo, componente o sistema funcione antes de que ocurra un fallo.
El tiempo medio para fallar se calcula de la siguiente manera:
Por ejemplo, en una oficina 7 bombillas alumbran un total de 300 horas y en ese lapso fallaron las 7
MTTF = 300 hrs. / 7 fallos
MTTF = 43 hrs.
¡Ojo! Es importante tomar en cuenta que para calcular esta métrica debemos tomar los datos de unidades idénticas (en este caso, bombillas).
El tiempo medio para fallar es importante porque permite:
> Predecir fallos: ayuda a estimar cuánto tiempo puede operar un equipo o componente antes de que ocurra un fallo.
> Tomar decisiones informadas: es una métrica valiosa a la hora de decidir cuándo reemplazar un equipo, si es rentable repararlo o es mejor invertir en uno nuevo.
> Cumplir con la normativa: en algunas industrias reguladas, como la aeronáutica o energía, el MTTF es crucial para cumplir con los estándares de seguridad y mantenimiento.
Representación gráfica de los indicadores de disponibilidad en la gestión de mantenimiento. -
Órdenes de Trabajo en retraso
Esta métrica mide el número de solicitudes de mantenimiento que no han sido completadas dentro de un plazo establecido o que están pendientes por ejecutarse.
Puede parecer muy simple pero es capaz de revelar problemas profundos en la gestión de mantenimiento y servir como base para la mejora continua.
Las órdenes de trabajo atrasadas pueden deberse a múltiples factores como:
> Falta de personal o recursos.
> Demoras en la entrega de repuestos.
> Priorización incorrecta de tareas.
> Sobrecarga de trabajo.
Para calcular el número de órdenes de trabajo en retraso basta con hacer el conteo de las órdenes que están pendientes de ejecución o que no se completaron en el plazo establecido.
Sin embargo, también podemos calcular el porcentaje de órdenes de trabajo atrasadas en relación con el total de órdenes de trabajo generadas. Se calcula de la siguiente manera: -
Tiempo medio entre mantenimientos preventivos (MTBM)
Es una métrica que es clave para evaluar la frecuencia de las actividades de mantenimiento planificadas y optimizar los programas de mantenimiento preventivo.
El MTBM indica cuánto tiempo pasa, en promedio, entre dos actividades de mantenimiento preventivo en un activo.
El tiempo medio entre mantenimientos se calcula de la siguiente manera:
MTBM = Tiempo total de operación / Número de mantenimientos preventivos realizados
Es un indicador clave de rendimiento que aporta valor en las empresas pues permite
> Aumentar la disponibilidad de los equipos: al reducir paradas no planificadas.
> Tomar decisiones informadas: proporciona datos para saber si es necesario ajustar el plan de mantenimiento.
> Optimizar los intervalos de mantenimiento: permitiendo ajustar la frecuencia de los mantenimientos preventivos para evitar intervenciones innecesarias o para reducir fallos por falta de mantenimiento. -
Tasa de falla observada
Es la relación entre el número total de activos con falla y el tiempo total acumulado durante el cual este conjunto de activos fue analizado.
Por ejemplo, si se producen 10 fallos en una máquina que funciona durante 20.000 horas, la tasa de fallos se calcularía de la siguiente manera:
Tasa de fallos = 10 fallos / 20.000 horas = 0,0005 fallos por hora
La tasa de falla observada es fundamental para comprender la frecuencia con la que se producen las fallas. Las tasas de fallas permiten planificar el mantenimiento, mejorar los diseños y aumentar la confiabilidad.
Cómo monitorear los KPIs de gestión de mantenimiento
Si bien ahora conoces algunos KPIs de mantenimiento que puedes incluir en tu gestión, es importante también el saber ¿cómo hacerlo? ¿Cómo lograr rastrear estos KPIs de manera efectiva? Una forma sencilla es a través de un software para mantenimiento de equipos como Linkaform el cual te permite realizar una gestión efectiva del mantenimiento de equipo.
Linkaform es un software y App que puedes utilizar desde una computadora personal hasta por medio de un smartphone, por lo que todos los datos se quedan almacenados en la nube de forma segura.
Dentro de la plataforma podrás administrar tus catálogos de piezas, máquinas o activos; podrás crear formularios digitales que te permitan realizar la recolección de información en campo, visualizar registros de servicios realizados, mantenimientos predictivos y correctivos, generar reportes de mantenimiento de manera automática o crear tus órdenes de trabajo y asignarlas a tus técnicos en campo. Además de contar con un dashboard en donde podrás personalizar los KPIs de mantenimiento que deseas monitorear.
Linkaform permite optimizar la operación de las empresas a través de la automatización de procesos. Por ejemplo, si un técnico en campo realiza una órden de trabajo a un equipo el cual tiene un valor que exceda el permitido, automáticamente envía un reporte vía correo electrónico al encargado, para poder priorizar la tarea de mantenimiento correctivo.
Si deseas conocer más información de Linkaform haz clic aquí o si deseas hablar con uno de nuestros expertos, agenda una demostración haciendo clic aquí.
Temas
- Servicio y mantenimiento (44)
- Crecimiento y liderazgo (40)
- Tecnología (23)
- Inspecciones y auditorías (20)
- Noticias (14)
- Control de visitas (13)
- Facility Manager (11)
- Promotoria (8)
- Seguridad (8)
- Control de accesos (6)
- Orden de trabajo (3)
- digitalización (3)
- Bitácoras (1)
- CIO (1)
- Checklist (1)
- Contabilidad (1)
- Gastos de Viaje (1)
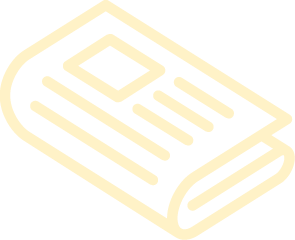
Suscríbete a nuestro Blog y recibe noticias de Linkaform una vez al mes.